Above: Earles forks on three BMW motorcycles.
by Jeff Dean
Today is
- A forklift (also called lift truck, jitney, fork truck, fork hoist, and forklift truck) is a powered industrial truck used to lift and move materials over short distances. The forklift was developed in the early 20th century by various companies, including Clark, which made transmissions, and Yale & Towne Manufacturing, which made hoists. Since World War II, the use and development of the.
- Clutch Release Fork This is the arm or lever that the linkage operates that moves the release bearing. There are several different styles of release arm. The most common in automotive use is the fork type that pivots on a rocker.
Find fork arm stock images in HD and millions of other royalty-free stock photos, illustrations and vectors in the Shutterstock collection. Thousands of new, high-quality pictures added every day.
The Earles fork was a variety of leading link fork where the pivot point was aft of the rear of the front wheel — this was the basis of a patent for the design. Designed by Englishman Ernest Richard George Earles, this triangulated fork actually caused the front end of a motorcycle to rise when braking hard — the reverse of the action of a telescopic fork. It was designed to accommodate sidecars, and from 1955 to 1969, BMW used the fork even though most of its motorcycles were sold as solo bikes. See Earles' 1951 patent application at the bottom of this page. Perhaps the greatest benefit of the Earles fork in sidecar use was its adjustability for rake and trail. The swinging arm pivot had two positions. Moving it to the forward position reduced trail, allowing the bike to turn with less effort when a sidecar was attached. The photos below shows the Earles fork as used by a British company, Douglas motorcycles, on its 1950s vintage, opposed-twin, 348cc Dragonfly model, two of only 1,600 built. Notice that this Earles fork has only one swing-arm pivot point, unlike BMW's forks, so it was intended only for solo usage, and was not adjustable for sidecar use. The motorcycle manufacturer that produced the most Earles-fork equipped motorcycles clearly was Munich-based BMW. Ironically, in 1935 it was the first manufacturer to produce oil-dampened telescopic forks on a production motorcycle, on the R12 and R17, which it then abandoned for the Earles fork. (Note: The first motorcycle equipped with hydraulic front forks was the 1934 R7, a concept machine that never went into production.) The Earles fork was most useful in sidecar-equipped motorcycles, but the vast majority of BMW's Earles fork bikes were sold as solo machines.From the 1956 through the 1969 model years, most of its motorcycles — both twins and singles — came with Earles forks. These models included the R26, R50, R60, R69, R27, R50/2, R50S, R60/2, and R69S. Above: A BMW R60/2 on the left, and an R69S on the right, both with Earles forks. Note that the swinging arms are mounted in the rear pivot points, which is appropriate for solo motorcycles. For sidecar use the swing arm is moved to the forward pivot point (other changes would be required as well, such as different rear drive gears, a different speedometer ratio, and stiffer suspension units). Above: A factory diagram of the R69S Earles fork from the 1966 BMW Instruction Manual on the left and an original blue R50/2 on the right. Click on the diagram to read “Technical Data” pages from the 1967 owners manual Below: Where is the world's only “Earles Fork Road?” It is the home of Bench Mark Works, founded by Craig “Vech” Vechorik, which supplies parts for vintage BMW riders all over the world. This noted road is in Sturgis, Mississippi, southwest of Starkville:
|
Forklift Fork dimensions: Forklift forks, also known as tines or blades, are used to lift and carry loads. They are an integral part of the forklift and ensuring you are using the correct ones and that they are in good condition is essential to both the safety of personnel, but also the forklift and the load.
Contents
Forklift fork dimensions and specifications
- Forklift blades: Horizontal part of the fork which lifts and supports the load
- Tip: End of the blade that is inserted to the load
- Shank: The vertical part of the fork
- Heel: Part of the fork where the shank and blade meet
- Hook: The hooks are the elements on the shank that support the forks on the forklift.
- Pin lock (or locking pin, latch pin). Positioned on the top hook and used to position the forks on the forklift carriage. The forklift fork pin can be a latch or button (mushroom) type.
- Taper: The difference in thickness between the tip and the heel. Tapers can begin at the heel or anywhere along the blade.
Production standards for all forks are based on common key- features:
Innovative and highly automated production process.
- Prime quality steel offering good welding characteristics and strong resistance to wear.
- Automated welding of upper and lower hooks with a robotic system, granting the better quality of the welding, quality repeatability, and higher process speed.
- Complete heat treatment with hardening and tempering on the entire fork, providing the best quality and reliability characteristics.

Standard forklift dimensions

- General: Fork correct dimensioning and conditions are essential for safe, cost-effective and damage-free pallet handling operations. Therefore, a regular fork inspection system should be put in place to ensure perfect operating conditions. Inspections, repairs or replacements shall be carried out as a pair.
- Height difference in fork tips: Check a pair of forks mounted on the fork carrier to detect a difference in tip heights. If the difference in tip heights exceeds 3% of the blade length, the pair of forks shall be withdrawn from service.
- Wear: Forks must be checked regularly to ensure the heel thickness is not less than 10% of the original thickness as per ISO 5057. If the fork thickness is less that 10%, the fork must be replaced or rerated.
Forklift fork inspection
- Inspections: Forks in use shall be inspected at intervals of 12 months or less depending on the possible severe application, multi-shift operation and fork conditions. Regular inspections should be carried out by trained personnel. In case of detected damage, failures, deformations, etc. forks shall be withdrawn from service and not be returned to service unless satisfactorily repaired or rerated.
- Cracks: Check visually inner heel and top and bottom hook areas to detect possible cracks. Apply non-destructive crack detection tests if necessary. If surface cracks are detected, forks should be withdrawn from service.
- Straightness: Check the straightness of the upper face of the blade and the front face of the shank. If the deviation exceeds 0,5% of blade length or shank height, fork shall be withdrawn from service.
- Angle: Check the fork upper face of the blade to load the face of the shank. If the fork has a deviation greater than 3 degrees from original specifications, fork shall be withdrawn from service
- Locking devices: Check the fork positioning locking to ensure their normal operation and wear conditions. If any fault is found, fork shall be withdrawn from service.
- Marking: Forks shall be marked with the nominal capacity and load center according to ISO 2330. If marking is not clearly legible, fork shall be withdrawn from service.
- Hooks: Check the fork hooks for possible wear, damage and cracks. If the clearance between fork and fork carrier is visually excessive, forks shall be withdrawn from service.
Replacement forklift forks
Repairs and tests: Repairs should be decided or carried out by authorized, expert personnel only, in accordance with recommendations of fork manufacturer. Do not repair surface cracks or wear them by welding. In case of repairs requiring fork re-setting, forks should be subjected to an appropriate heat-treatment. Fork subjected to repairs different from repairs or replacements of the positioning lock and/or marking can only return to service after having passed a yield test as described in ISO 2330.
Forklift pre shift inspection
The best way to inspect forks is to use a fork caliper.
- Determine the nominal thickness of “N” of the fork. Measurement has to be done on the fork shank using the caliper ruler.
- Position the caliper at the end of the heel internal radius with the opening corresponding to the nominal dimension “N” (eg. for N 45 use 45 mm thickness), where the wear is higher.
- If the fork enters the opening, it is mandatory to replace it. DANGER OF BREAKING. Furthermore, a 10% reduction in fork blade thickness results in a 20% reduction in operating capacity

Types of forklift forks
Following is a list of some of the special types of forklift forks, used for specific applications.
- Pin Type & Bar Type: the forks have a guide and are attached to a shaft. Found on larger lift trucks and construction machines such as some telehandlers. Pin-Types can come with a lower hook
- Drum handling forks: these forks have a section cut out of the side of the forks to enable a drum to be lifted
- Coil handling forks: the inside edge of the forks are “chamfered” to provide a surface for the coil to sit on.
- Explosion-proof: if the forklift is to be used in explosive environments then the forks are clad in stainless steel to prevent sparking. The stainless steel coating is typically 2mm thick
- Forks for the food production industry: forklifts that are used in the food industry are typically clad in stainless steel as they are regularly washed down to maintain cleanliness.
- Lumber forks: have a thin and wide blade for ease when inserting into loads
Lifting equipment
The lifting equipment on forklift trucks machines is characterized by robust and high-quality design and numerous options combined with excellent visibility. Forklift trucks can offer many different types of masts all of the clear view design. In combination with forks and/or attachments, it can provide the handling solution to meet your needs.
For even better handling, there are also a number of intelligent functions for forklift machines:
- Pre-selected lifting height – the operator can simply find the right lifting height by means of 15 pre-selected lifting heights.
- No chain slack – the chains are kept tensioned at all times, eliminating undesired movements of the forks or the attachment.
- Vertical hold– the automatic tilt device ensures that the load is taken up and put down vertically to the loading surface.
Forklift Masts Types:
- Single-stage mast forklift
- 2 stage mast forklift
- Quad mast forklift
What type of steel is used for forklift forks?
What type of steel is used for forklift forks?They are made of different types of steel. Sometimes HSLA A572-50 (high strength low alloyed) steel, 1045-1060 heat-treated material, T1 heat-treated steel, and others.
What are the forklift forks used for?The forks on a forklift are used to make direct contact with a load for transport. They are attached to the forklift carriage and are designed to carry a load from the bottom. Forklift forks come in all shapes and sizes. There is a wide variety of fork types available for various applications.
What is a quad mast forklift?4-Stage – A quad or four-stage mast is designed for very high stacking. Quad masts allow for a shorter collapsed height when compared to a three-stage with equivalent MFH (maximum fork height).
What are the Forklift dimensions?What size forklift should I get for my warehouse?
It is often a question asked by business owners and operation managers. Forklift Dimensions can be tricky and unique to every application. Virtually every forklift dimension could potentially impact an operation, and create a safety hazard if not specified correctly and carefully.
The most read
Forklift Safety Procedures
Fork Arm Wear Caliper
Forklifts are extremely useful workplace vehicles, as long as they are used safely and appropriately by operators who are appropriately trained and competent to use them. Learn about the rules for driving forklifts.
Telescope Fork Arm
Forklift Brands
Forklift Brands and models: Which forklift brand is best? Top brands in the world: Caterpillar, Toyota, Volvo, Hyundai, forklift brands and models, top 10 forklift brands.
Fork Arm Extension
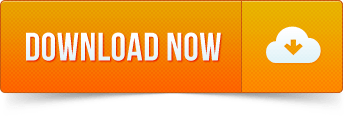